
A Guide to a Total Fluid Management Service
Jump to a Chapter
Chapter 1 | An introduction to the drilling fluid management process →
Chapter 2 | Steps to take before operations start →
Chapter 3 | Drilling fluid management and on-site engineering while drilling →
Chapter 4 | Understanding solids control and the drilling mud cleaning process →
Chapter 5 | The closed-loop drilling process →

An introduction to the drilling fluid management process
CHAPTER 1
Selecting the best drilling fluid system is an important consideration when designing and implementing a successful drilling operation. Drilling mud helps maintain wellbore integrity and protects the producing formation by balancing formation pressure. It cools and lubricates the drillstring and bit, transports drilled cuttings to the surface, supports the wellbore until casing is set, and can power a downhole directional motor during drilling and sliding operations.
Unlike other oil and gas technological advances, the evolving technology around fluids is less understood. Today’s drilling fluid systems can be complicated to manage. They employ equipment furnished with the drilling rig mixed with add-on equipment—specially sourced—depending on the formation or the rig’s drilling system. Some of the various drilling rig systems that involve fluids include:
-
Mud tanks, shale shakers, vacuum degasser, desander, desilter, centrifuges, and other associated equipment that remove the solids from the fluid
-
Instrumented surface measurements for monitoring the fluid system during drilling operations
-
Closed-loop systems for solids control
-
Haul-off and disposal service
The drilling fluid system touches almost every part of the drilling program. Having the experience to understand the well being drilled, selecting the best equipment for the level of service provided, and adapting this equipment to the existing system can be a challenging task. You need experienced people who know the equipment, have a defined operational process, and excel in logistics. Extracting the most value from the system, including haul-off and disposal, is the challenge facing operators today. This is indeed a formidable task.
Drilling fluid management services
Because the drilling fluid system touches so many drilling activities, it makes sense that these related processes be managed as an overall system. What is a drilling fluid management service? It is a combination of the right equipment, systems and expertise that provides maximum value to the operator in a safe and environmentally sound manner.
This can include complete mud systems and performance packages that account for every situation that may be encountered during the drilling process. Strategic planning and trained field technicians to ensure that your operation starts and ends according to plan. Built-in contingencies that can address any unforeseen events. A total fluid management service—from fluid system selection to solids control and engineering to trucking and disposal services—that eliminate headaches and streamline processes.
Overall savings are worth additional system costs
Drilling today’s complex wells is expensive. While in some cases, the cost of a total solutions package may be incrementally more expensive, savings can be realized through reduced equipment footprint and associated costs at the drill site, reduced waste management costs, and reduced liability concerns. If taken as a whole, a drilling fluid management program can help operators realize significant savings per well, shaving days from their drilling program while further enhancing the goal of a successful operation.
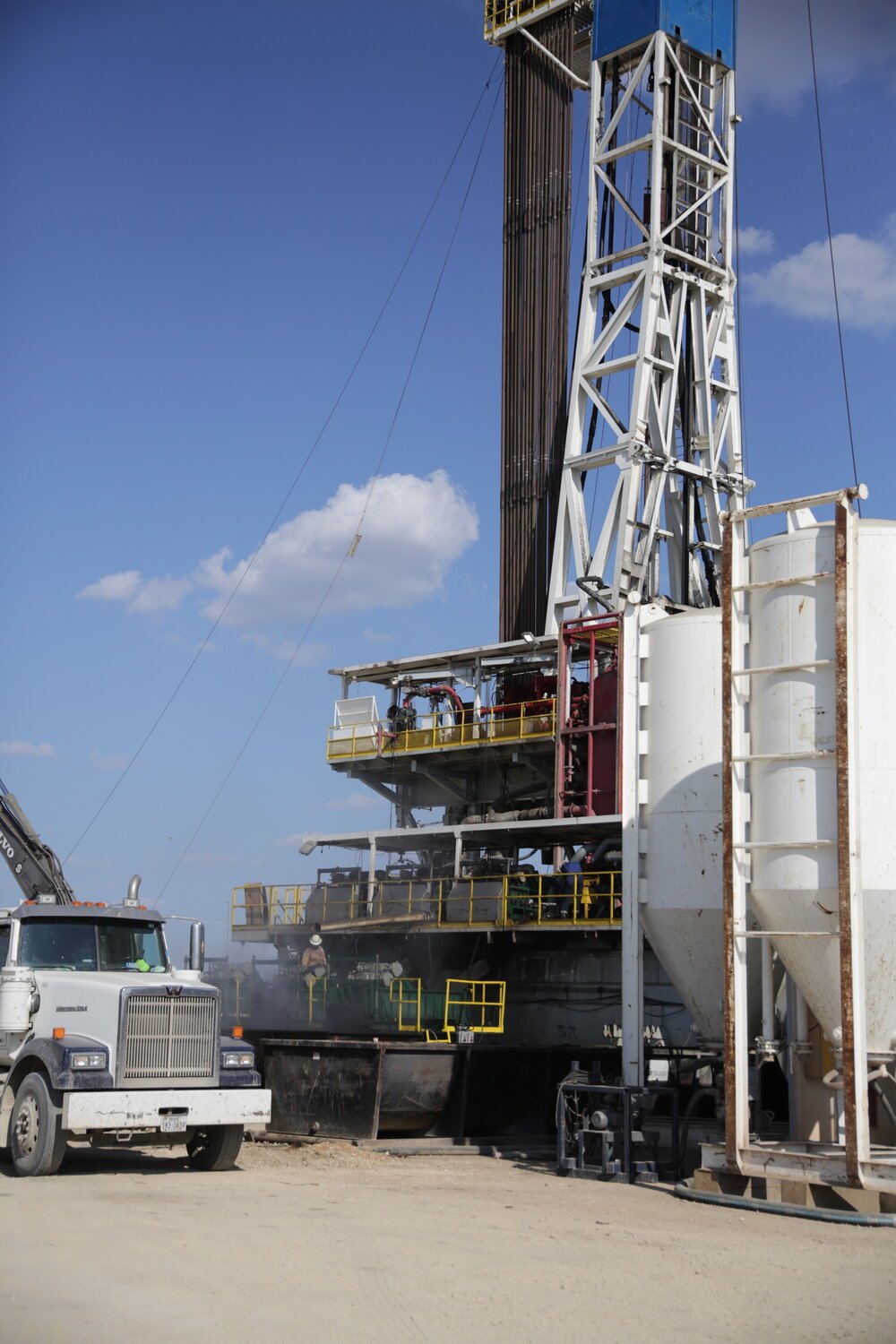
In addition, overall reduced drilling costs can be achieved through efficiencies and collaboration. Beating the curve by multiple days results not only in a successful job but significant cost savings to the operator. Working together as a team can make this happen. It is critical to have the right systems, people, and equipment in place for your well to:
-
Improve overall well efficiency
-
Reduce overall drilling costs
-
Extend the life of fluids
-
Deliver less non-productive time (NPT)
-
Drill the well safely
-
Reduce liability concerns
-
Achieve environmental compliance
What follows in this guide is a step-by-step approach to establishing and managing a complete drilling fluid management program. We cover the steps required to make fluid management successful and impactful, including operational and day-to-day best practices, an explanation of solids control and the closed-loop process, and finally the importance of a sound haul-off and disposal program. Follow this link for a list of common terms used to describe drilling fluids and additives, and dive into drilling fluids in depth with this link to industry resource guides.

Steps to take before operations start
CHAPTER 2
It is estimated that drilling fluids costs average 10% of total well construction costs. While this figure may seem like a small percentage, the drilling fluid system connects to almost every other drilling system on the rig. The right fluid management system can enhance economics (improve recovery and decrease NPT), reduce both liquids and solids waste, all while protecting the environment and addressing regulatory concerns. But the wrong system, incompatible equipment or inexperienced personnel can cause drilling or formation problems that can easily increase overall well costs.
Regardless of whether you are planning basic mud and monitoring services or an entire fluid management program, pre-job planning is crucial to the operation. From system design to logistics to equipment hook-up and testing, it is critical to have a sound fluid program in place prior to drilling.

Planning is a crucial part of a successful drilling fluid maintenance program
Designing the proper fluid system depends on many variables. The design of the well, depth, formation, type of rig, and overall drilling budget all contribute to the type and complexity. Other deciding factors include:
-
State or local regulations that mandate the use of a closed-loop system
-
Drilling on government land (where a closed-loop system is a must)
-
Proximity to residential areas
-
Environmentally sensitive areas such as nearby waterways or marshes, where risk to the local environment from a conventional reserve pit is greater or where open reserve pits are not allowed
-
Complex setups, such as closed-loop systems and haul-off and disposal, where expertise is needed to manage the overall system
-
Operations where the operator wishes to outsource fluids management
What is the optimal fluid system for the well?
During the bid process, the fluids company examines many factors affecting the mud system to determine the most efficient program. This may include offset well information, recap reports of nearby wells, the formation and type of well being drilled, the well schematic, and mud types commonly used in the area. The operator may also have specific requirements such as an oil-based mud, water-based mud, or brine system.
Drilling fluid selection requires thorough well planning, expertise and experience. Factors to be considered in selecting drilling fluids include formation geology, temperature and pressure; expected drilling performance; and the type of rig and any additional fluid-related equipment. Financial impact must also be considered when selecting fluids, as oil-based fluids are generally more expensive than water-based fluids.
In high-pressure, high-temperature (HPHT) drilling environments, defined as pressure greater than 15,000 psi (103.43 MPa) and temperature greater than 350°F (177°C) in the American
Closed-loop system for solids control
There are many reasons for selecting a closed-loop system. It may be required for the area being drilled. The operator may want to take advantage of the reduced waste and cost savings. There are many steps to take regardless of the situation. Equipment must be sourced and ordered and then adapted to the current rig and fit into the existing well footprint. The expected amount of solids is determined based on well depth, type of mud, hole size, and intervals. The amount of solids will also affect the number of trucks needed for haul off.
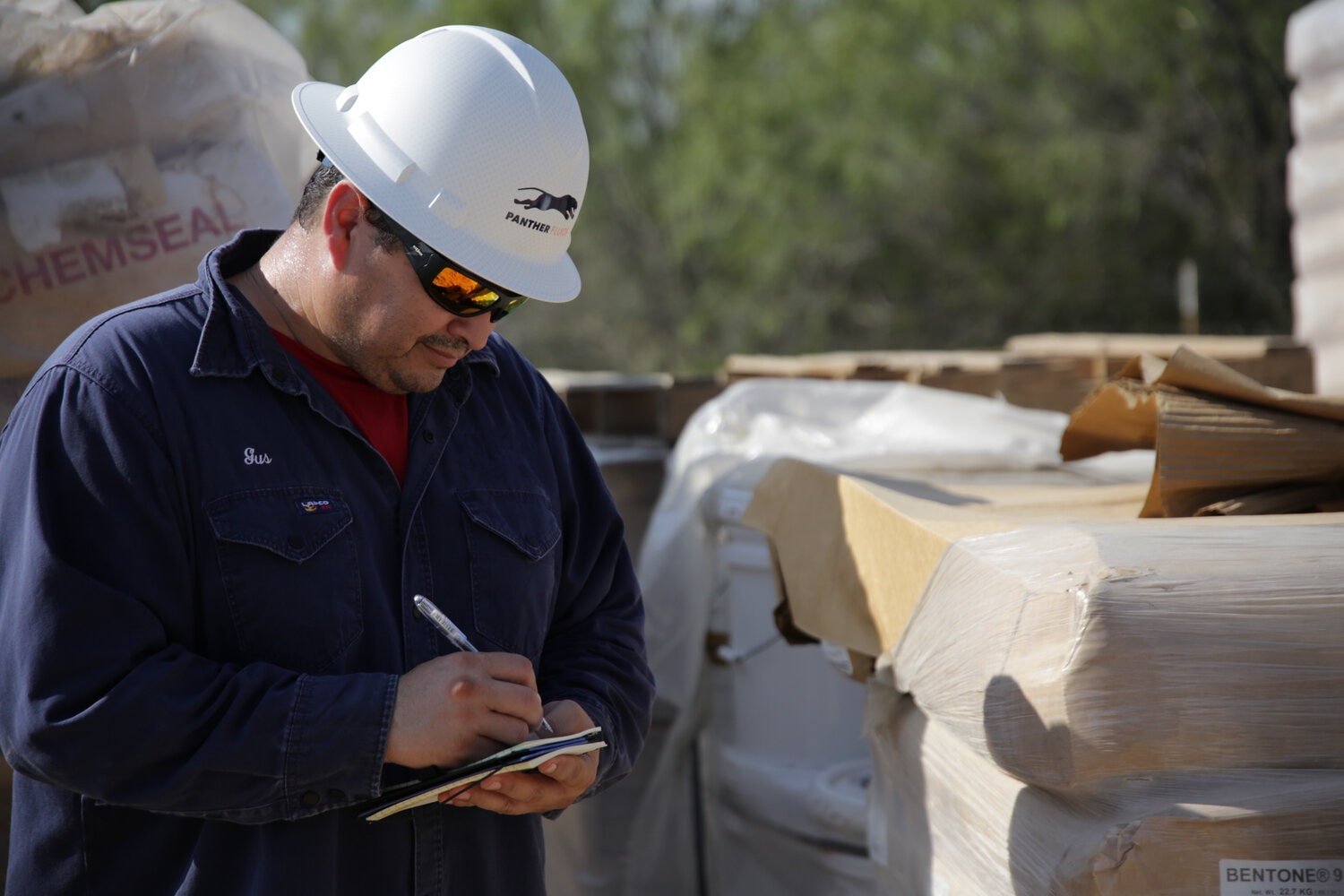
Equipment considerations
For a closed-loop system, additional tanks, centrifuges, screens, and shakers may be needed that bring up a new set of logistical considerations. All equipment needs to be sourced, ordered, and fit onto the existing well pad. Power requirements for the additional equipment will have to be determined and accounted for. Heavy logistics such as delivery, connecting to the existing rig, and testing need to be scheduled and completed. Is time allotted for these additional steps? Finally, all equipment must perform to published specifications and have undergone the latest maintenance checks.
Onsite expertise is critical
Flexibility and response to unexpected issues or scenarios are important with any drilling fluid program or service company. Having the experience and knowledge to respond correctly and solve the issue is critical. Hence the importance that the person leading the fluid program and coordinating activities with the solids control expert and the drilling team have knowledge of the formation, fluid system and rig. Ideally, they have worked on similar systems previously and have completed all safety and equipment certifications. The right team, equipment, and system allows the operator and their personnel to focus on the well with the confidence that the fluid system is in good hands.
Fluid logistics and supplies
Once the fluid system is determined, the mud, additives, chemicals, and other supplies need to be sourced, ordered and delivered. Local facilities should be stocked with what is needed for the well. Once all items are delivered, a wellsite inventory check is recommended. Additional contingency planning must be made for unexpected events. Also, the ability to modify the fluid program to enhance the solids control plan is critical to improve efficiency.
Will mud be mixed on site or delivered by vendor?
Some systems can be mixed on site while others are delivered by the vendor. This depends on many factors such as the type of system (water-based mud is more easily mixed on site, while oil-based mud is typically delivered pre-mixed). If mixing on site, additional tanks may be required.
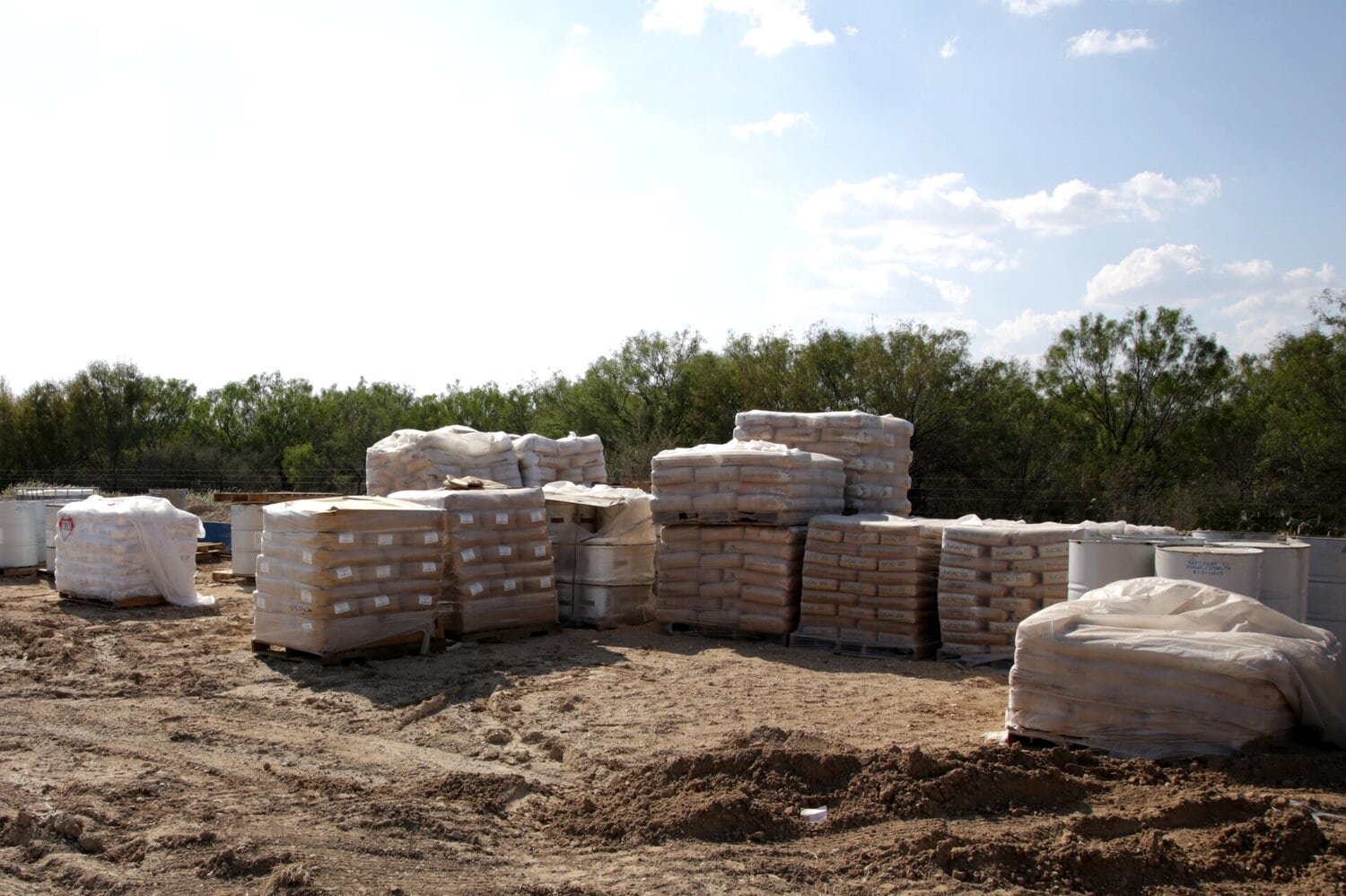
Haul off and disposal
Safe and incident-free disposal of cuttings and fluids is a requirement while drilling the well and once drilling operations are complete. There are two options for solids disposal:
-
Land farms, where cuttings are ground, treated and worked into the soil
-
Injection, where the cuttings and fluids are injected into an underground cavern or disposal well
Transporting the cuttings and liquids to the disposal site involves more than just hiring a qualified trucking company. The nearest disposal site, road conditions, the cost of trucking and disposal (and its effect on the overall budget), and the type of truck (open, covered, completely sealed) all must be factored in. Regulatory issues such as permits, manifests, and end-of-well reports are needed depending on local regulations. All activities must be performed in an environmentally responsible manner.
Safety
The goal of any wellsite program is to complete operations with no safety incidents, minimal NPT, and no environmental impact. To help achieve these goals, verify that all wellsite personnel are certified for equipment usage and expected well conditions and that any special training (high pressure or H2S) is completed prior to starting the job.
The same applies to equipment. All equipment should be rated for expected temperatures and pressures and all maintenance checks performed. Can the closed-loop system handle the expected amount and size of returns? Are all permits in place for haul off and disposal? Lastly, do all third parties (trucking, disposal site) have all safety and regulatory certifications in place?
While a total fluid management program may entail additional initial costs and planning, benefits to the environment and the operator’s bottom line can be greater.

Drilling fluid management and onsite engineering while drilling
CHAPTER 3
Once day-to-day drilling operations begin, the focus of drilling fluid management moves to the drilling fluids engineer. The fluids engineer prepares the daily mud reports for the driller and operator, communicates with the solids control expert to maintain the solids control output, and makes changes to the fluid plan in case of unexpected events. The goal is to keep the fluid system operating at maximum efficiency.
Daily mud check

Mud weight and viscosity are checked regularly for changes that can affect the mud plan. The drilling fluids engineer combines this information into the daily mud reports which contain drilling data (well depth, bit size, pit volume, and pump data) and mud properties (weight, pH, viscosity, and solids content). An increase in flow, increase in cuttings or differences in the size of the cuttings, or returns showing gas or saltwater may indicate formation issues. When this happens, additives or chemicals may need to be added to adjust mud properties to keep them within the plan.
Additional testing includes a retort test to determine the solid percentage of the particles. In some cases, mud may be sent to a testing lab for particle size analyses (PSA) to determine if dilution needs to be increased.
Flexibility to modify the fluid program to enhance the solids control plan
Throughout the drilling process, mud returns are checked to verify the fluid system is performing to plan. Screen size needs to be monitored and adjusted to remove the maximum amount of cuttings while allowing fluid through the screens. However, ultrafine size particles affect mud properties adversely because of their large surface-to-volume ratios. By consulting with the solids control expert and drilling team, the system can be adjusted to ensure optimal removal of low-gravity solids that can negatively affect the rheological properties of the mud.
Weight up schedule
Certain formations may need a heavier mud weight. These changes in mud weight are determined by the operator and noted in the fluid plan. As mud weight is increased, the mud engineer is responsible for maintaining the desired drilling fluid properties by adding additives or chemicals. A change in mud weight also affects the solids control equipment and system. For example, screens and centrifuge speeds may be adjusted for optimal solids removal to run a more cost-effective operation.
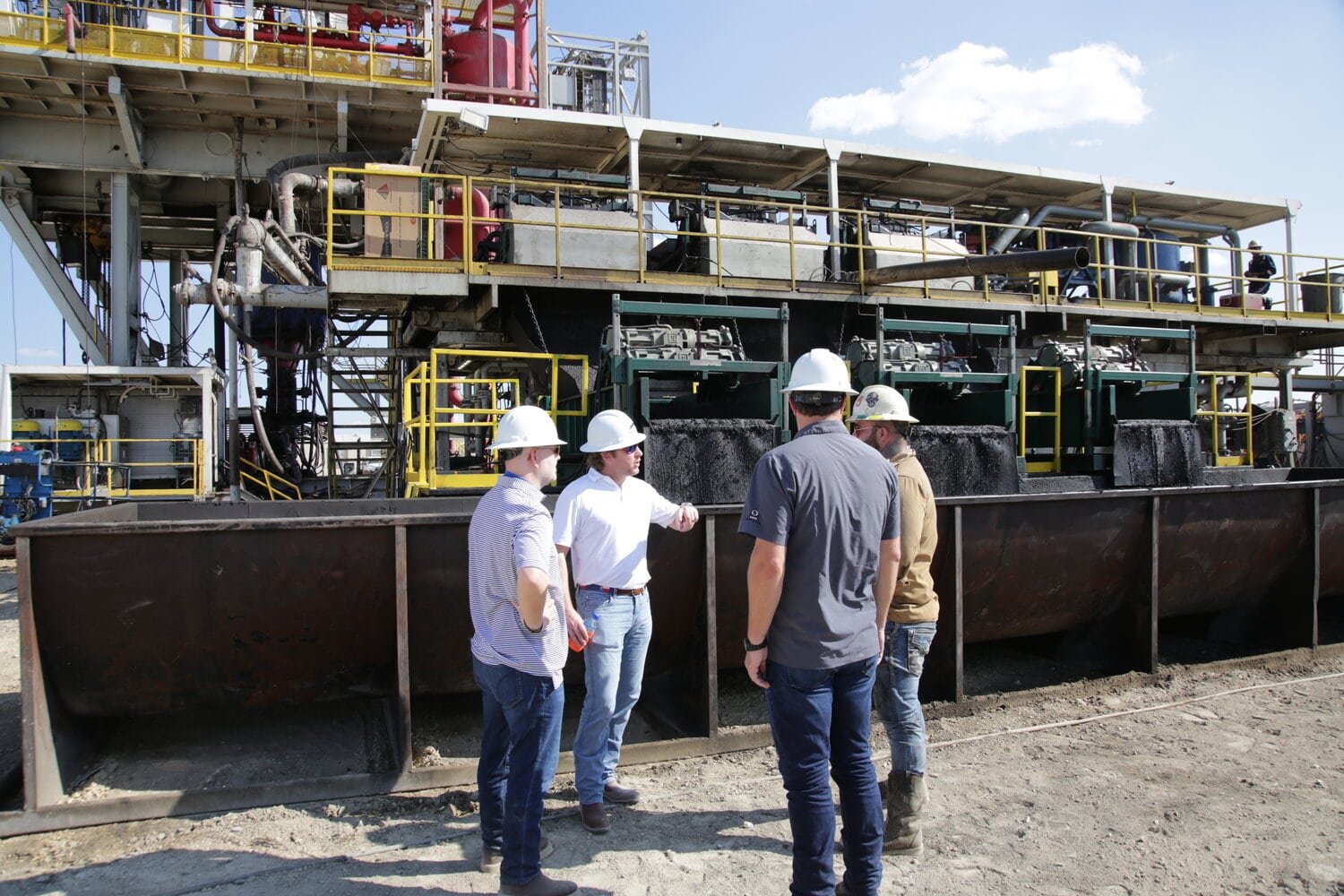
Importance of monitoring and maintaining fluid properties while drilling
Another task of the drilling fluids engineer is to maintain mud properties as the new hole is drilled and mud volume is increased. Dilution volume is added to the mud to control solids and to maintain volume as the new hole is drilled. Maintaining a stable hole environment sustains hole integrity, controls reactive shale, and maintains a consistent mud system when encountering contaminants.
Equipment maintenance
In addition to selecting and integrating the equipment on site, a total fluid management service involves monitoring the mud circulating system around the clock with qualified, full-time personnel. This includes 24/7 monitoring of flow rates for system efficiencies, system checks such as taking samples for solids content, checking underflow and overflow, and preventative maintenance such as repairing/replacing the shaker screens.
.jpg?width=450&height=301&name=Z3C65093%20(1).jpg)
Collaboration and communication are key to successful operations
Close collaboration between the drilling fluids engineer, solids control expert, and drilling team is crucial to get the best results. The goal is to fine tune the system to remove the maximum amount of cuttings, recondition the maximum amount of fluid for reuse, and reclaim barite, diesel, and other elements with the least dilution possible. It is the responsibility of the drilling fluids engineer to monitor fluid properties and maintain them according to the drilling fluid program. Fluid properties also indicate formation or fluid changes which must be treated accordingly. Drilling events that affect the mud program, whether expected or not, need to be quickly addressed to keep the mud program within the plan. The result is maximum efficiency and cost savings.
Throughout the drilling phase, a sound fluid program can help address any issues that arise whether expected or unexpected. Onsite drilling fluids experts can oversee the fluid program and provide an efficient total fluid management service.

Understanding solids control and the drilling mud cleaning process
CHAPTER 4
A sound solids control system effectively and efficiently separates the drill cuttings from the drilling fluid and is an integral part of a drilling fluid management system. While there are many considerations, including determining the right system, equipment selection, and integration with the drilling rig and drilling program, many benefits can be obtained that result in full system efficiencies.

-
Reduce the amount of solids content in the mud
-
Reduce disposal, both amount of liquids and solids
-
Reduce costs of drilling fluid maintenance, clean up, and disposal
-
Help achieve environmental and regulatory compliance
-
Help lower fluid dilution rates
-
Reduce the volume of required additives
-
Allow higher flow rates
-
Extend the life of the drilling fluid
Equipment considerations
Additional equipment such as cuttings tanks, centrifuges, screens, and shakers is needed for the solids control system. The equipment needs to be sourced and ordered and then setup and tested once delivered to the wellsite. All maintenance checks should be performed, and certifications should be in place. State permits for the trucking company must be in order.
-
Different types and correct number of centrifuges based on well schematic and mud weight
-
Adequate number of drying shakers based on what is needed and what is currently available on the rig
-
Trackhoe and cuttings tanks based on the amount of solids expected per well
-
Adequate number of trucks and number of total loads per well; the expected amount of solids is based on well depth, type of mud, and hole interval size, and the number of loads will depend on the capacity of each truck
During drilling
The solids control system separates solids from the mud with each step resulting in finer particles being removed for disposal.
The first step in solids recovery is the rig shaker, which removes the larger particles of drill cuttings from the slurry returning from the well
Drying shakers further decrease the amount of liquid retained on the drill cuttings. Once this step is performed, drill cuttings are loaded in trucks, removed from the rig site, and disposed at a permitted disposal site
The drilling fluid exits beneath the rig’s liquid shaker and is processed through the hydrocyclones to remove more particles
Upon exiting the hydrocyclones, the fluid is then processed through the centrifuges (one or more depending on mud weight) which remove even finer particles
Once through the centrifuges, the clean mud is returned to the mud system
During drilling, the solids control process must be continuously monitored by the drilling fluids engineer to ensure the following:
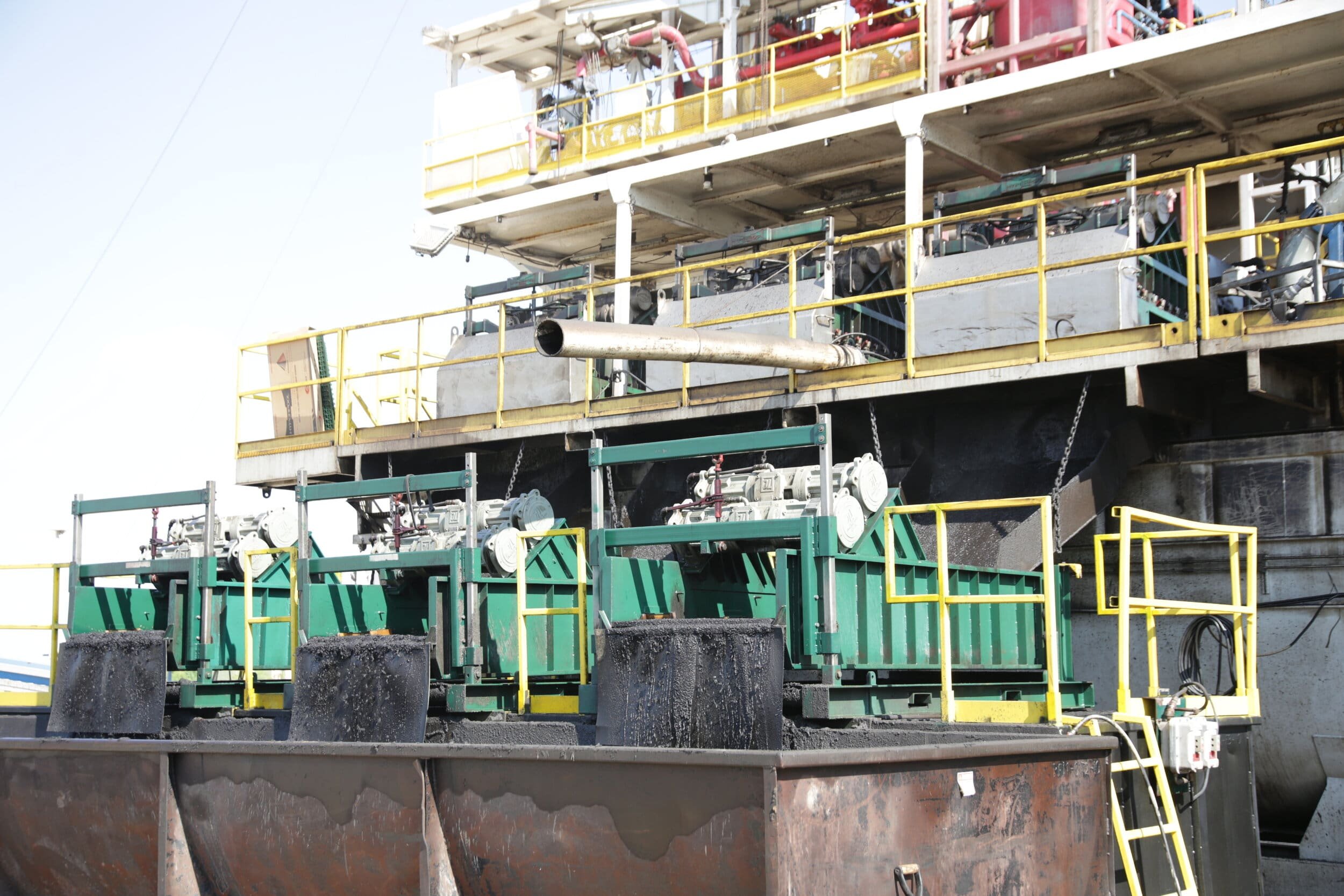
-
Maintain the optimal system balance between clean fluid and the amount of solids introduced
-
Monitor and test as required to maintain fluid properties
-
If the mud weight changes during drilling, adjust the system by fine tuning the centrifuge(s) and adding dilution to remove the optimal amount of cuttings
-
Have trucks on hand and ready to go as solids accumulate and manage truck logistics (hours, departure/arrival) during drilling
Barite and its effect on the solids control system
Barite is used to weight the mud in intervals where a heavier mud is needed. However, the weight of barite impacts the solids control system and affects the speed and number of centrifuges needed to remove ultra-fine cuttings. Typically, one centrifuge is used for mud weights lighter than 12 lb/gal. A second centrifuge is utilized for reclaiming the barite. The goal is to remove the maximum amount of solids while returning as much barite to the system as possible.
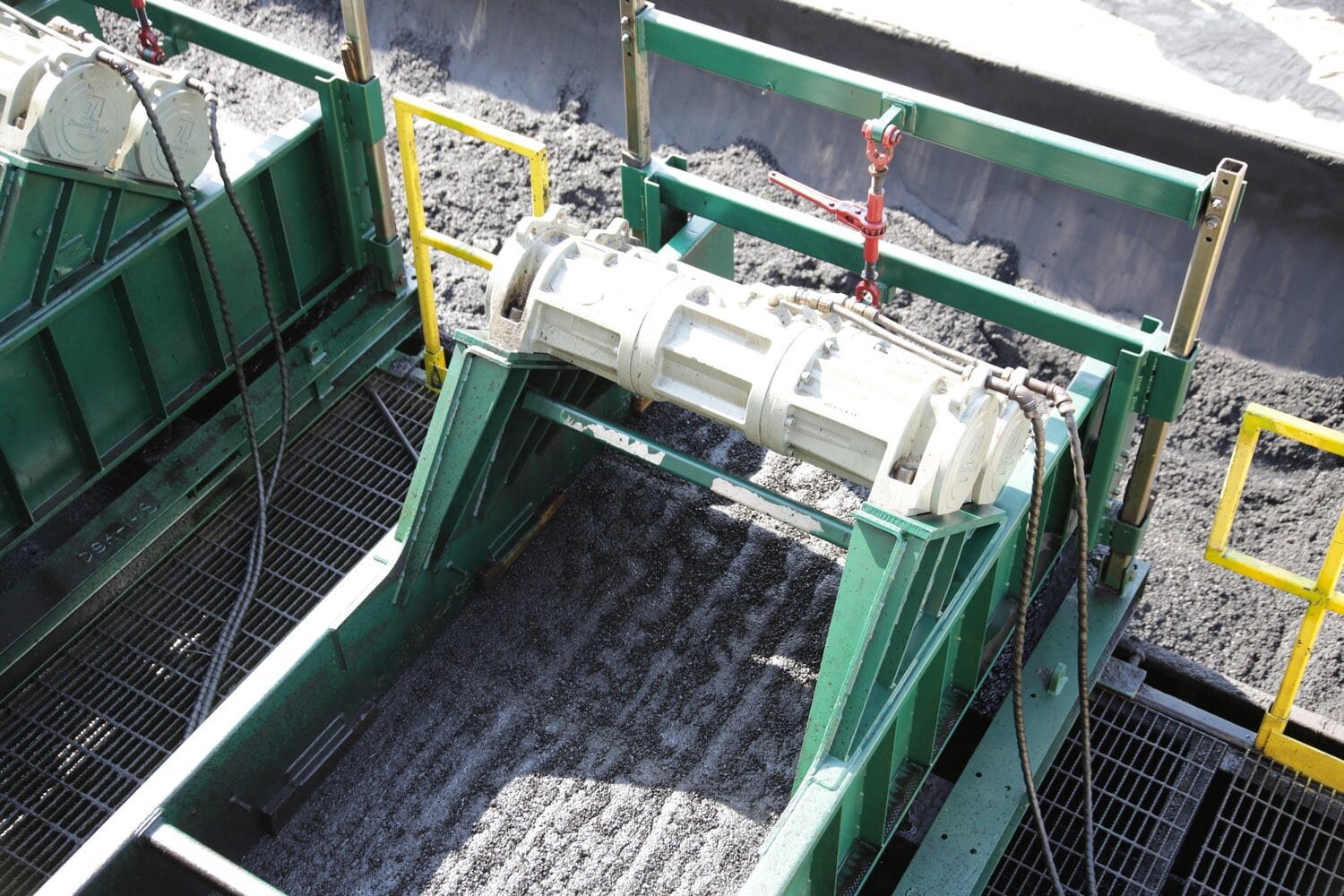
Importance of solids control expert
Collaboration between the mud engineer, the solids control expert, the drilling team, and the operator is essential. Working together, they maintain the solids concentration, keeping it to a low level. This combination can streamline the process to make the total system as efficient as possible for the operator while reducing well construction costs.
While a solids control system provides many benefits to the operator and can enhance overall solids removal effectiveness, the next phase in fluid management is the introduction of a closed-loop system for increased environmental control and reduced risk of drilling fluid spills.

The closed-loop drilling process
CHAPTER 5
In recent years, new regulations have limited the use of open pits at the wellsite. As environmental regulations tightened, and open pits became a bigger liability, closed loop drilling systems became the preferred solution for many operators. Today, regulatory and environmental concerns have made solids control and closed-loop systems an important part of drilling operations. While initial well construction costs can be higher using these systems, there are many benefits that can result in an overall improvement in well economics.
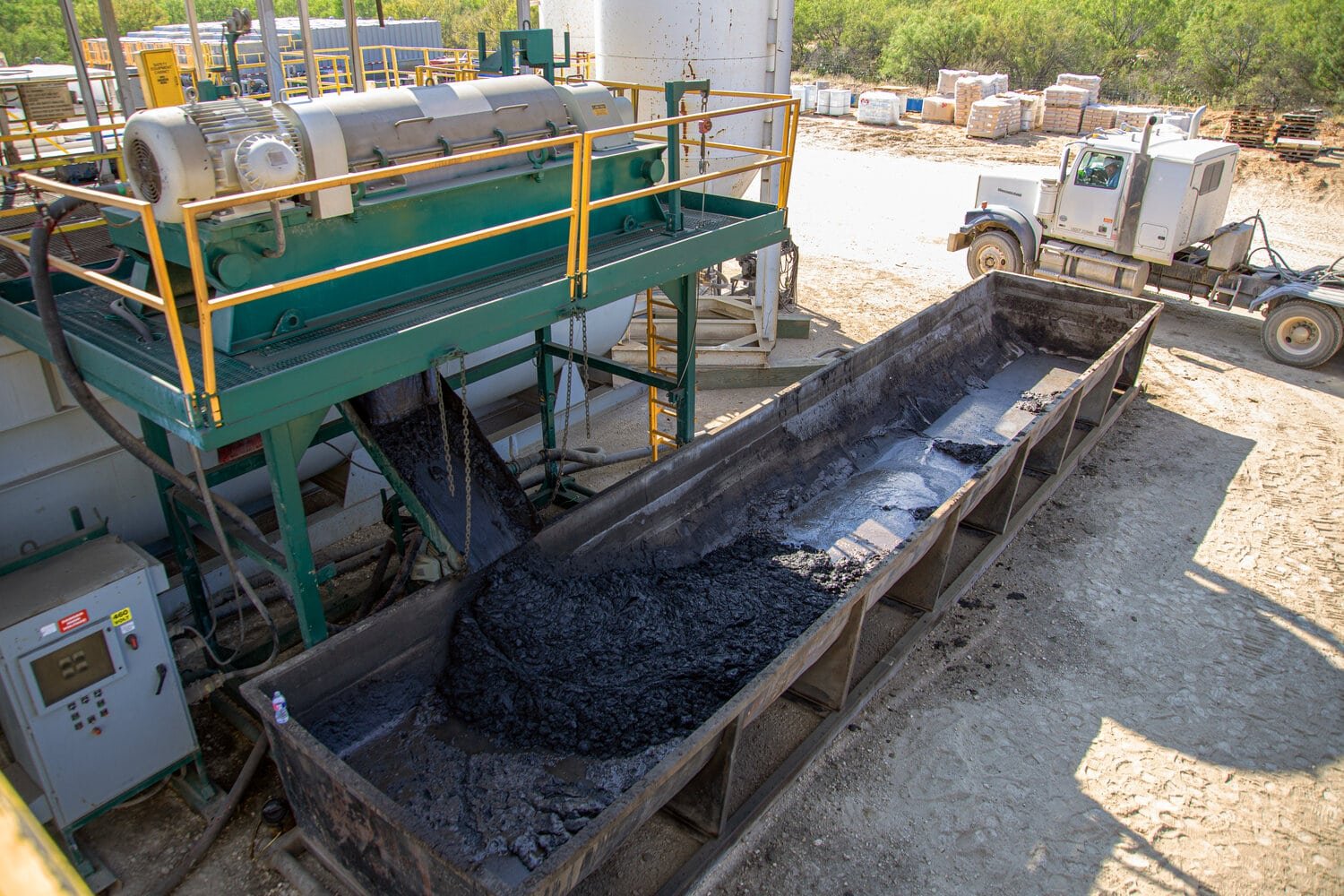
-
Decreases liabilities associated with the impact to land and water due to pit failures
-
Decreases environmental issues
-
Helps ensure regulatory compliance
-
Helps eliminate risk of soil, surface water, and groundwater contamination
-
Reduces waste volume and waste disposal fees
-
Reduces total drilling mud costs
-
Decreases well footprint
-
Eliminates cost of pit construction and lining
In a closed-loop drilling system, all cuttings and fluids are captured, processed, and discharged without the use of any open pits. All cuttings are hauled off and disposed while fluids are reconditioned, cleaned, and processed then returned to the mud system. A closed-loop system can be utilized with any type of drilling fluid—oil-based, water-based, brine or synthetic—on most any type of rig and for any formation or well type.
Using a closed-loop system makes the most sense when:
-
A closed-loop system is mandated by the landowner, state, or local regulations
-
Drilling on government land
-
Drilling in or near a residential area
-
Drilling in or near environmentally-sensitive areas (nearby waterways, marshes, game sanctuary) where risk to the local environment from a conventional reserve pit is greater
-
There is potential for surface water or groundwater contamination and associated liabilities
-
Drilling shallow wells where the cost of building an open pit is not economical
-
Wells are spudded with a water-based mud and then switched to an oil-based mud system
-
Wells utilize an oil-based mud system
-
Offshore operations using a diesel- or mineral-based fluid must include a closed-loop process for continuously capturing all drilled cuttings and returning them to shore for regulated disposal
Protecting the environment and adhering to all regulatory controls have made solids control and closed-loop systems a key option during drilling operations. Closed-loop systems can minimize and mitigate the risks associated with open pits by eliminating soil and groundwater contamination and removing the clean-up and remediation costs that may be incurred. However, closed-loop systems can be complex. Proven onsite expertise with the system, equipment, and process is needed to make sure the system runs properly.
Equipment space considerations
Closed loop systems adapt the mud system equipment that is already on the rig. Typically, 600 bbl of storage capacity is needed to replace the volume of the open pit, so tank size and selection are important. The space available for any additional equipment is always limited at the wellsite making pre-planning and logistics critical. On a typical rig footprint, the mud tanks are located approximately 60 ft away from the wellbore. An additional 50 to 60 ft is needed to allow adequate space for truck logistics. Because trucks will be hauling cuttings while drilling is underway, there must be room for loading and maneuvering in a safe manner.
Economics for a closed-loop system when spudding a well
Some wells are spudded using a water-based mud system and then switched to an oil-based mud later in the drill plan. Because the oil-based cuttings must be removed and disposed of once the switch is made, it makes economic sense to utilize a closed loop system from the start to save the cost of constructing an open pit.
A closed-loop drilling system can eliminate or dramatically reduce the use of open pits. Closed-loop systems are environmentally sound, can lower overall well construction costs, decrease liabilities from spills and leaks, and decrease regulatory concerns. A closed-loop system enhances the efficiency of the solids control system and can improve drilling operations by helping increase ROP and decreasing fluid loss. Once the solids and liquids are separated, the next and final step is removing the waste from the rig site to a permitted disposal site.

Haul off and disposal, safety, and compliance
CHAPTER 6
A total fluid management program includes the haul-off and disposal of all fluids and drill cuttings. If a closed-loop system is used, disposal begins during drilling as cuttings accumulate. Proper haul-off and disposal keep companies in compliance with governmental regulations. It also avoids the risks of ground and water contamination, improper disposal, and other issues that can linger long after the well enters production. Some key selection considerations for proper transport and disposal include:
-
A fully vetted disposal site with all permits in place
-
A certified and permitted trucking company with an outstanding safety record
Disposal methods
Safe and efficient disposal of cuttings and fluids is critical to the overall success of the project. The most popular methods of mud and cuttings disposal are landfarms and injection. Other methods include biodegradation, incineration, and solidification.
Landfarms
The landfarm process involves tilling the cuttings and mud into the surrounding soil of a licensed property. Landfarming reduces organic and inorganic particles through dilution, biodegradation, and absorption. Bacteria in the soil help biodegrade hydrocarbons under anaerobic conditions. The landfarm must be licensed to accept disposal and must be located away from residential, environmental, and groundwater areas.
Injection
In this process, cuttings are ground to fine particles, mixed into a slurry, and injected into a well or cavern. The well or cavern must have all proper permits in place, and the local groundwater horizons must be avoided.
Biodegradation
Biodegradation uses microorganisms to biologically degrade cuttings and mud. It utilizes a nitrogen source for bacterial growth, continual dilution, and an odor suppressant. The mixture of cuttings/mud and bacteria must be frequently turned to introduce oxygen to the process. The process is relatively slow and cannot handle large volumes of cuttings.
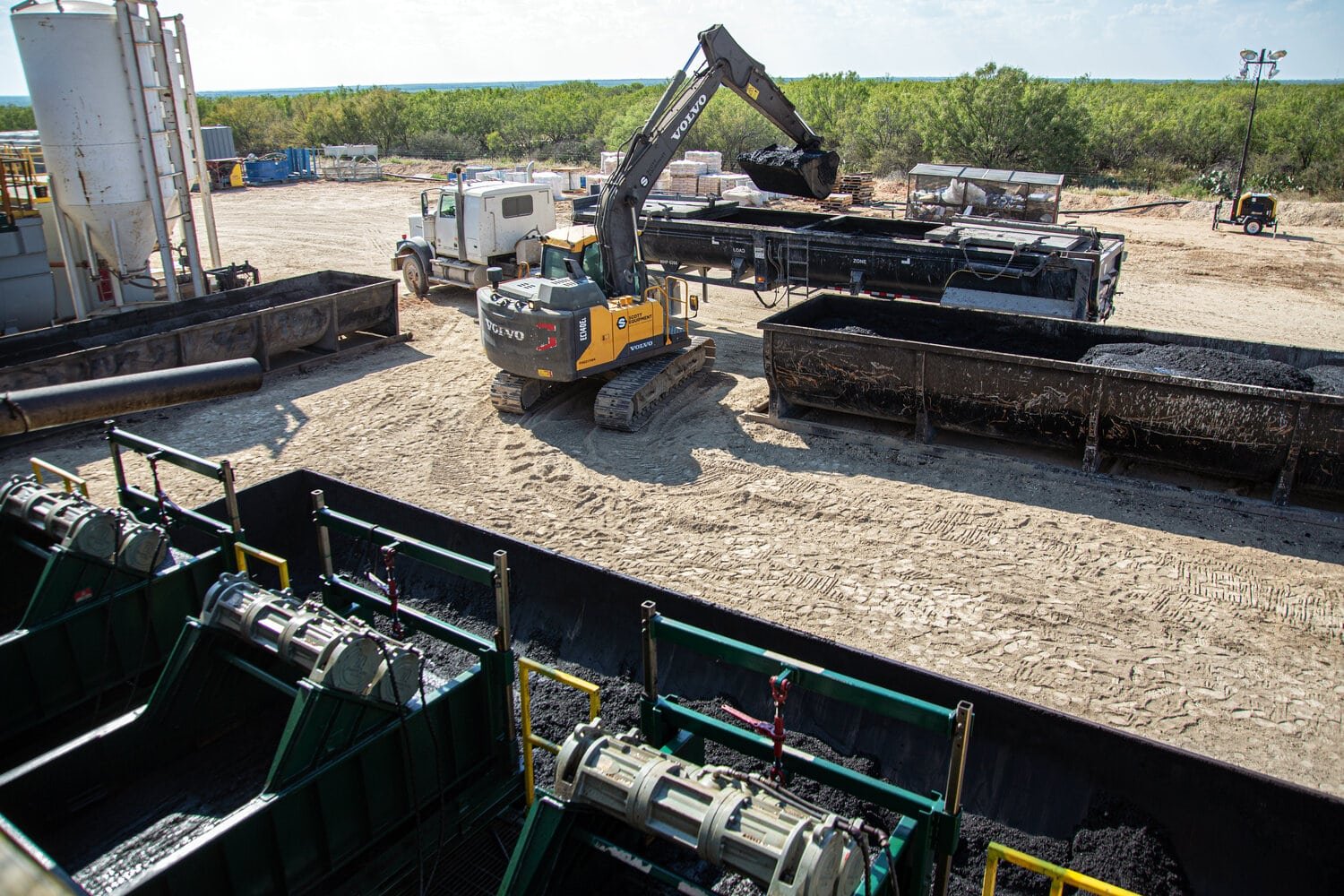
Incineration
Thermal systems are used offshore to burn drill cuttings. Due to the resulting air emissions, safety concerns of the heat source, and high efficiency required, this is not a widely used disposal method.
Solidification
In this process, disposed cuttings and mud are mixed with a solidification agent to form a concrete-like solid. The solid product can be repurposed for uses such as road construction or disposed at an authorized disposal site.
Regardless of the method of disposal, you must keep abreast of the latest regulations, both local and state, to ensure conformance throughout the disposal process. This includes all the related paperwork that must be completed to fully document the disposal process.
Oil-based mud reconditioning and reuse
After the job, oil-based mud is typically returned to the supplier. However, the mud must maintain the original properties, usually within a percentage of the original mud specification. If mud is out-of-spec then it may need to be reconditioned before returning.

Trucking
Transporting the cuttings and liquid to the disposal site involves more than just hiring a qualified trucking company. Factors involved in transporting cuttings and fluid include the location of the nearest disposal site, the best route and road conditions, the cost of trucking and disposal (and its effect on the overall budget), and the type of truck (open, covered, completely sealed). All paperwork must be in order, including permits and manifests; and end-of-well reports are needed depending on local regulations. All of these activities must be performed in an environmentally-responsible manner.
The best executed job will be considered a failure if the fluids and cuttings are not disposed of properly. A total fluid management plan, including haul off and disposal, should be committed to remaining incident-free, safe, and reliable throughout the process.

Results
CHAPTER 7
As the oil and gas industry has grown more complex and competitive, the margin for error has decreased considerably. The right fluid system can make the difference between a successful job and one that is fraught with problems, demanding time and resources from the operator. It’s important for operators planning on a total fluid management solution to choose a company with the experience and knowledge to run a successful program.
Panther Fluids Management combines drilling fluids engineering with logistics management to reduce well costs, ensure regulatory compliance, and simplify the administrative burden. The result is an innovative fluid management service that results in top performance from your drilling program.
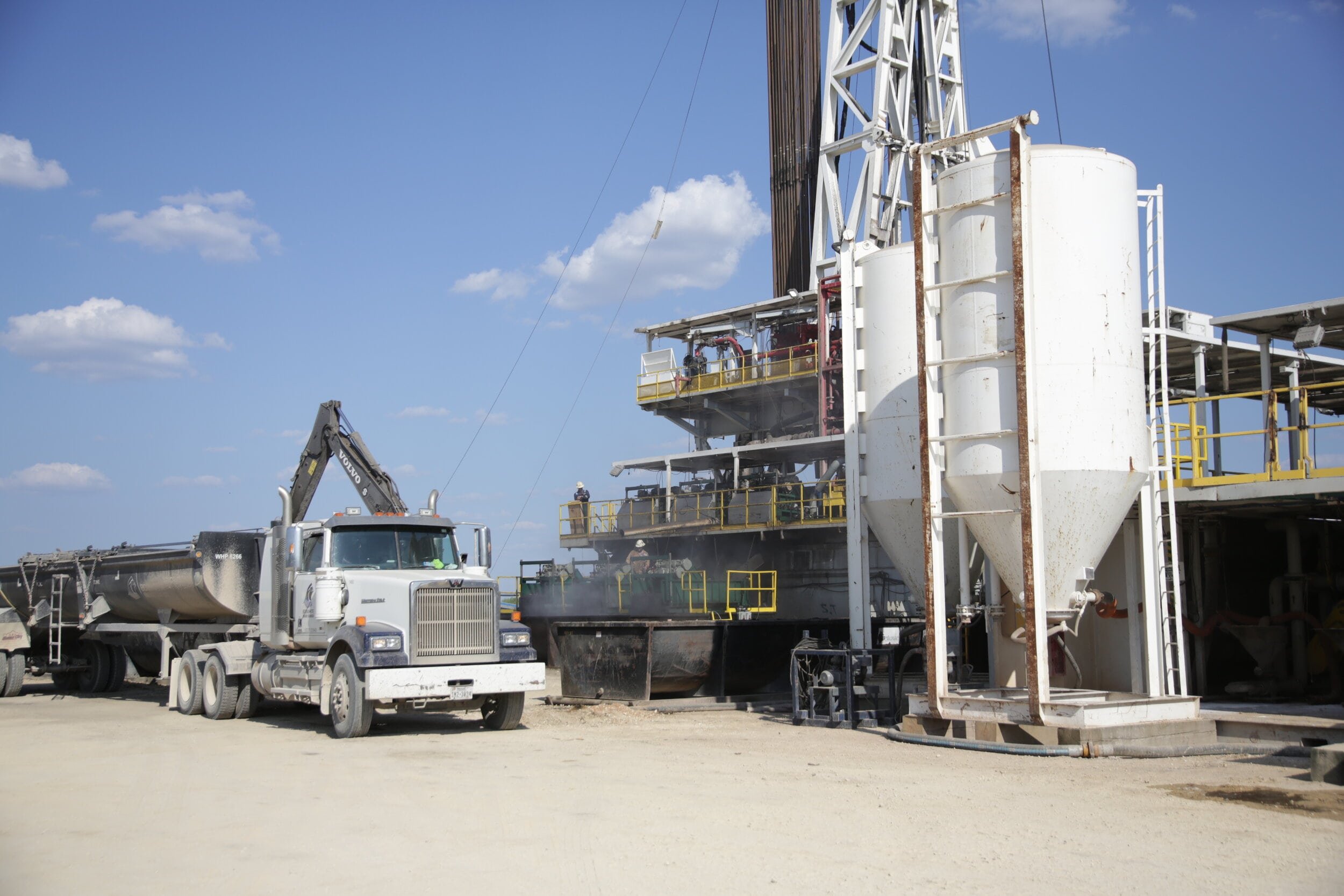
-
We have the experience to evaluate your plan, work with the operator and drilling company, and recommend the best drilling fluid program for the well.
-
We have the knowledge to select and engineer a drilling fluid system with the most innovative, cost-effective equipment available. If we don’t have the specific piece of equipment, we can find it through our network of suppliers.
-
With the Panther team at your wellsite, operations run more smoothly. We monitor and maintain the system, whether it’s the drilling mud, separators and tanks, or a complete closed-loop system for solids control. With our in-depth knowledge and experience, we can plan for any contingencies or issues that may arise.
-
We complete every job by performing efficient and safe haul-off and disposal, conforming to all local, state, and environmental regulations. Our knowledge and experience is essential to recognize and mitigate the risk involved with a total fluid life-cycle solution.
The result? Reduced drilling costs, less NPT, enhanced overall drilling efficiency, and top performance from your well. That’s the Panther Advantage™.
At Panther Fluids Management, our services don’t end when the drilling stops. Customers rely on us for expert advice and guidance throughout the well completion and production phases, too.
Consulting services
Our consulting services include experts on fluid systems, solids control and closed loop systems and haul off and disposal, as well as onsite fluid management. We can consult on every aspect of fluid systems from planning to disposal or can work with your company’s consultants or experts.
Tank selection
Tanks for storing and disposal of different wellsite fluids are an important part of any fluid management program. Wellsite operations employ a wide variety of tanks for drilling fluids, solids control, completion fluids and production chemicals. Types of tanks include open-top tanks, drilling-mud tanks, slope-bottom tanks, round-bottom tanks, and flat-bottom tanks. Tanks can be standard ordered or fabricated to your exact specifications and well footprint. Tanks can be rented, leased, or purchased.
Completion fluids
We can supply the appropriate fluids during completion or workover operations. Our wide range of fluids solutions can help control wellbore pressures and minimize formation damage. Panther can effectively design a completions fluid that considers the formation characteristics of your well.
Production chemicals
Once production is established, we can supply a full line of production chemicals and additives to help maintain production. Panther can identify the production problem, design an efficient program to restore or enhance production levels, and monitor and maintain proper production levels.
Together, our experts work with your team to ensure the success of your operation.

Contact the Big Cats Today!
We'd love to discuss your upcoming project.